Shale oil extraction
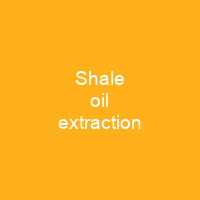
Shale oil extraction is an industrial process for unconventional oil production. It converts kerogen in oil shale into shale oil by pyrolysis, hydrogenation, or thermal dissolution. The industry shrank in the mid-20th century following the discovery of large reserves of conventional oil. High petroleum prices at the beginning of the 21st century have led to renewed interest.
About Shale oil extraction in brief
Shale oil extraction is an industrial process for unconventional oil production. It converts kerogen in oil shale into shale oil by pyrolysis, hydrogenation, or thermal dissolution. The resultant shale oil is used as fuel oil or upgraded to meet refinery feedstock specifications by adding hydrogen and removing sulfur and nitrogen impurities. The industry shrank in the mid-20th century following the discovery of large reserves of conventional oil, but high petroleum prices at the beginning of the 21st century have led to renewed interest. As of 2010, major long-standing extraction industries are operating in Estonia, Brazil, and China. Critics of shale oil extraction pose questions about waste disposal, extensive water use, waste water management, and air pollution. The composition of the oil shale may lend value to the extraction of the extraction process through the recovery of the kerogen through the endmicposition process. The oldest and the most common extraction method involves pyrofullysis. Burning the spent char off the shale produces oil shale ash. Spent shale and shale ash can be used as ingredients in cement or brick manufacture. In 2008, their industries produced about 930,000 metric tonnes of shaleOil. The last oil shale retort in the US, operated by Unocal Corporation, closed in 1991. The US program was restarted in 2003, followed by a commercial leasing program in 2005 permitting the extraction of oil shale and oil sands on federal lands in accordance with the Energy Policy Act of 2005.
Australia, the US,. and Canada have tested shaleOil extraction techniques via demonstration projects and are planning commercial implementation; Morocco and Jordan have announced their intent to do the same. Only four processes are in commercial use: Kiviter, Galoter, Fushun, and Petrosix. In this process, oil shale is heated in the absence of oxygen until its kerogen decomposes into condensable shale oil vapors and non-condense oil gas. Oil shale gas is then cooled, cooled, and added to condense oil to create shale oil. In oil shale processing produces spent shale, which consists of inorganic compounds such as pitch, asphalt, pitch and waxes. Heating the shale to a high temperature and completing the decomotherposition require a lot of heat. The earliest description of the process dates to the 10th century. In 1684, Great Britain granted the first formal extraction process patent. Extraction industries and innovations became widespread during the 19th century, but they shrank during the mid to late 20th century due to low oil prices. China, Estonia, New Zealand, South Africa, Spain, Sweden, and Switzerland began extracting shale oil in the early 20th Century. In 1944, the U.S. recommenced shale oil extracting as part of its Synthetic Liquid Fuels Program. These industries continued until oil prices fell sharply in the 1980s. In the early 1990s, the last oil fracking plant was closed in the United States. The first shale oil extractor was built in Australia, Brazil and Canada.
You want to know more about Shale oil extraction?
This page is based on the article Shale oil extraction published in Wikipedia (as of Nov. 01, 2020) and was automatically summarized using artificial intelligence.